- Joined
- May 3, 2007
- Messages
- 247
Lets see if I can crash some 56K
I wrote this a while back for the forum, thought it might help if it was in this thread since it was stickied. Hope no one minds. If so, ill remove it.
With all the interest in modding the lower end of the Tomahawk world, I decided to put together a quick rundown of how I mod, and assemble these Hawks.
First off, I realize that MANY members on this board build FAR superior Hawks than myself,and I by no means, mean to offend their work. This is just a step by step process of how I put them together and I thought some members could pick up some tips I have learned, as well as suggesting some to me that I may not have thought of.
Lastly, all of this work was done in my fathers and my shop. He is a retired Machine Shop Owner, and an old-school Machinist of the finest order. I realize that not everyone will have access to some of the tools and processes that I use, but nearly all of this can be accomplished with lesser tools, while still achieving the same end results.
I had to break this down into 2 different threads, as the forum will only allow 10 pictues per post.
Here we go.
I am doing this Hawk for a co-worker. He is full blooded Native American, and has agreed to trade me an authentic War Hammer in exchange for this Hawk. He wanted something simple, effective, and not very modern looking.
This is no stranger to you all, The CS Trail Hawk, in all its $19.95 Glory.
This was one of the better handles I have gotten as of late. Straight grain, and a ton of meat above the head.
First we will address the head. Inside the "eye" there is usually 1/8in of rollover material. If not removed, this will cause the head to grab the handle premature, and not allow for a good seat.
My weapon of choice to remove this is an air grinder with an abrasive stick.
A few rounds inside the eye, and we are looking good and smooth.
Next I hit the head with a small belt sander. I remove all the rough slag, and take off as much of the finish as I can. As well as remove that pesky "Taiwan" stamp. You know you hate it. The finish that CS uses is TOUGH.
Back to the handle for a bit. You can see where the rough inside of the head has gouged the handle from the factory, this is what we want to prevent. A few quick hits on the belt sander, and we will be good.
Ahh, a snug fit all the way around. This may take a few times of sanding, and eyeballing. You want there to be no gap between where the handle meets the eye.
Once we have a good fit, its back to head prep. A sandblaster is by far the easiest way to do this. It also provides a great surface for paint to adhere to.
After the blasting, I give the head a good bath in water and soap. Then, hit it with a coat of primer.
While that is drying, I decided to hit the handle with the ol Fire Wrench (torch) to add some character, and give it an aged look.
Continued in pt2.
I wrote this a while back for the forum, thought it might help if it was in this thread since it was stickied. Hope no one minds. If so, ill remove it.
With all the interest in modding the lower end of the Tomahawk world, I decided to put together a quick rundown of how I mod, and assemble these Hawks.
First off, I realize that MANY members on this board build FAR superior Hawks than myself,and I by no means, mean to offend their work. This is just a step by step process of how I put them together and I thought some members could pick up some tips I have learned, as well as suggesting some to me that I may not have thought of.
Lastly, all of this work was done in my fathers and my shop. He is a retired Machine Shop Owner, and an old-school Machinist of the finest order. I realize that not everyone will have access to some of the tools and processes that I use, but nearly all of this can be accomplished with lesser tools, while still achieving the same end results.
I had to break this down into 2 different threads, as the forum will only allow 10 pictues per post.
Here we go.
I am doing this Hawk for a co-worker. He is full blooded Native American, and has agreed to trade me an authentic War Hammer in exchange for this Hawk. He wanted something simple, effective, and not very modern looking.
This is no stranger to you all, The CS Trail Hawk, in all its $19.95 Glory.
This was one of the better handles I have gotten as of late. Straight grain, and a ton of meat above the head.

First we will address the head. Inside the "eye" there is usually 1/8in of rollover material. If not removed, this will cause the head to grab the handle premature, and not allow for a good seat.

My weapon of choice to remove this is an air grinder with an abrasive stick.

A few rounds inside the eye, and we are looking good and smooth.

Next I hit the head with a small belt sander. I remove all the rough slag, and take off as much of the finish as I can. As well as remove that pesky "Taiwan" stamp. You know you hate it. The finish that CS uses is TOUGH.

Back to the handle for a bit. You can see where the rough inside of the head has gouged the handle from the factory, this is what we want to prevent. A few quick hits on the belt sander, and we will be good.

Ahh, a snug fit all the way around. This may take a few times of sanding, and eyeballing. You want there to be no gap between where the handle meets the eye.

Once we have a good fit, its back to head prep. A sandblaster is by far the easiest way to do this. It also provides a great surface for paint to adhere to.
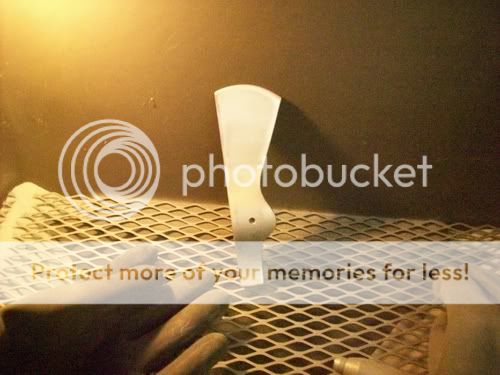
After the blasting, I give the head a good bath in water and soap. Then, hit it with a coat of primer.
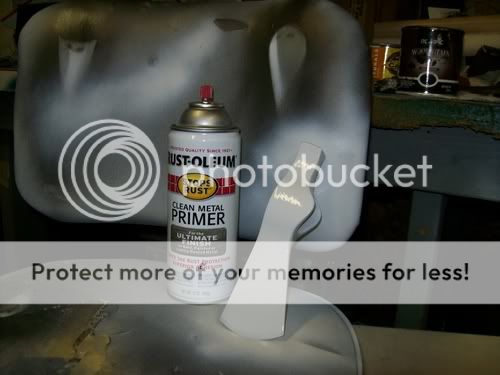
While that is drying, I decided to hit the handle with the ol Fire Wrench (torch) to add some character, and give it an aged look.

Continued in pt2.