- Joined
- Sep 29, 2009
- Messages
- 1,614
So decided to monkey with the guard a bit more to get an idea what it would look like bent. I took a piece of paper and cut it out the same size as the guard and bent it the way I was thinking and put it up against the knife and it still looked too big for what I'd like to see. So finally something went off in my head that said "hey dumbass, why don't you see if that metal cutting bandsaw and little grinder you have that are actually designed specifically to cut and shape steel can be applied in this situation?" Son of a gun! Wouldn't you know they actually do?
So I knocked down the guard a bit and I still have a little shaping to do it make it fairly equal looking on both ends of the oval, and if I can't I can always modify it a bit with those fancy machines I mentioned earlier.
So here is the other guard that was the same size that I put underneath to show how much I took off.
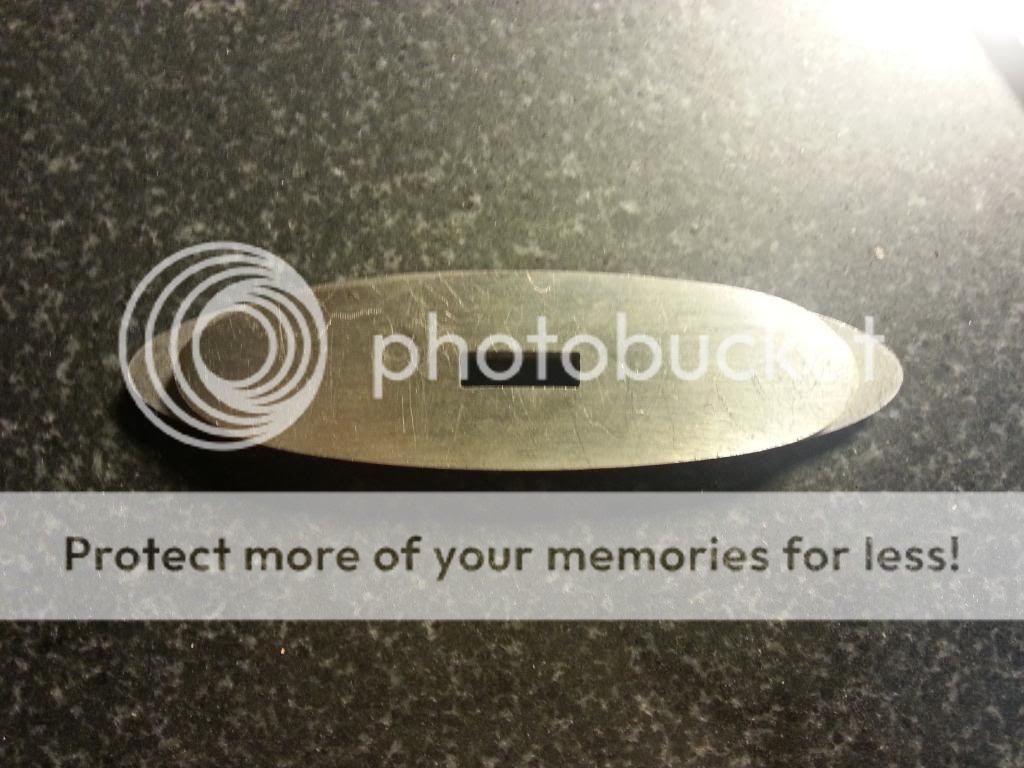
Here is a layout of it on the knife. Possibly still a tad long but I'll do another mock up and see if I need to make it smaller


So here is the other guard that was the same size that I put underneath to show how much I took off.
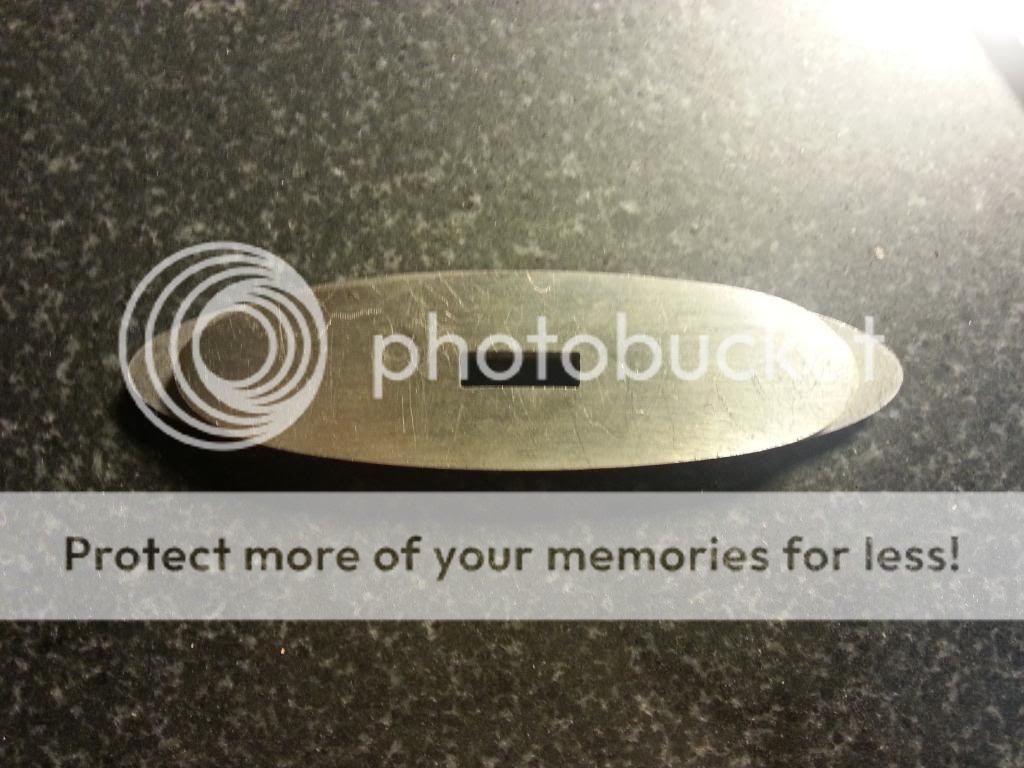
Here is a layout of it on the knife. Possibly still a tad long but I'll do another mock up and see if I need to make it smaller
