Bailey Knives
Knifemaker / Craftsman / Service Provider
- Joined
- Oct 18, 2004
- Messages
- 3,765
OK, here goes for the next section. It is time to make a welt. I have an old piece of leather that is not quite up to grade for a sheath, but is perfect for a welt. First I trace the sheath on the leather.
Then I cut the outer line
and highlight it with a thin sharpie so I can see the line
Here it is all cut out
and laid on the inside of the sheath for the first time.
I noticed that on the inside of the top of the sheath, the leather never really matched up, and when I went to sand down the outside of the edge, I had to take a lot of leather off the sheath in order to meet up with the welt. I am not sure if this makes sense, but in order to counteract this, I cut a small piece of the leather out so that it sits tightly against the inside top of the sheath, and still meets up with the outer portion of the sheath...ok I just confused myself by that statement, but here is a pic, maybe that will help.
When I did it, the welt stuck out of the sheath a little, and I had to move the notch up a little to make it fit.
This looks better
Here is where I am sure I will have the most eyebrows raised. I use rivets to hold the belt loop down. I know, I know...metal against the blade.
However, the hammer that I use has a convex face and when I pound the rivets from the inside, I put them a little recessed area just from pounding. I have never had a sheath returned to me or a knife for that matter because the rivets were marring the handle. Here is what I mean.
More in a bit...
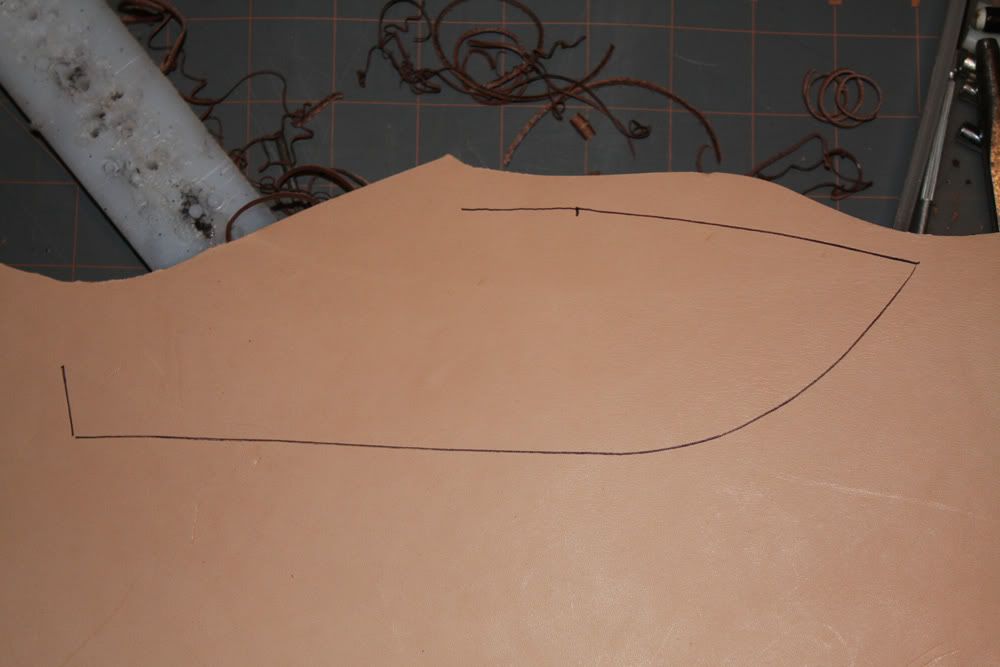
Then I cut the outer line
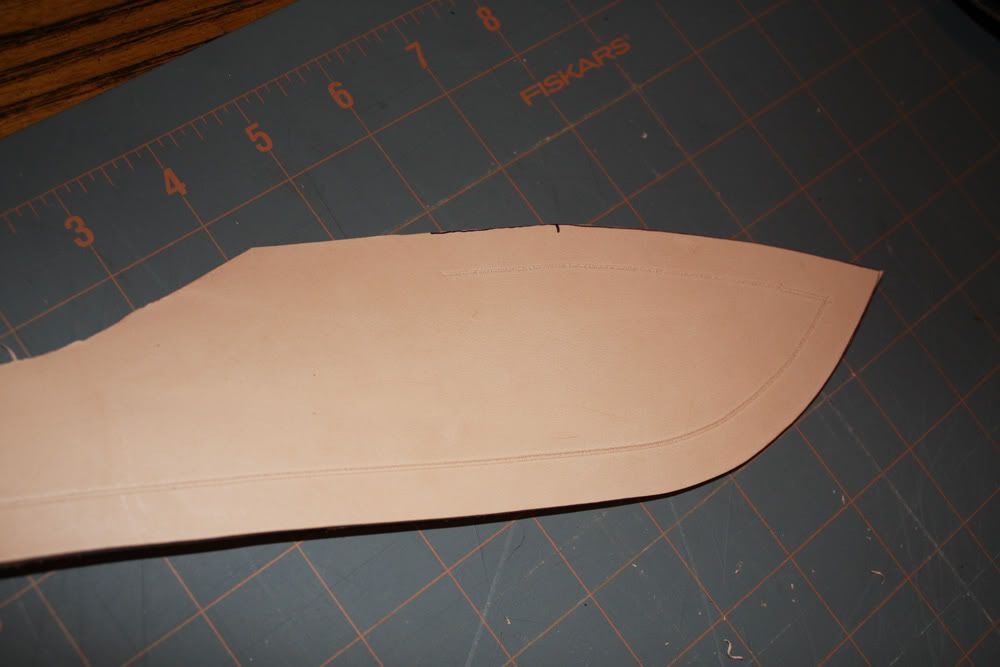
and highlight it with a thin sharpie so I can see the line

Here it is all cut out

and laid on the inside of the sheath for the first time.

I noticed that on the inside of the top of the sheath, the leather never really matched up, and when I went to sand down the outside of the edge, I had to take a lot of leather off the sheath in order to meet up with the welt. I am not sure if this makes sense, but in order to counteract this, I cut a small piece of the leather out so that it sits tightly against the inside top of the sheath, and still meets up with the outer portion of the sheath...ok I just confused myself by that statement, but here is a pic, maybe that will help.
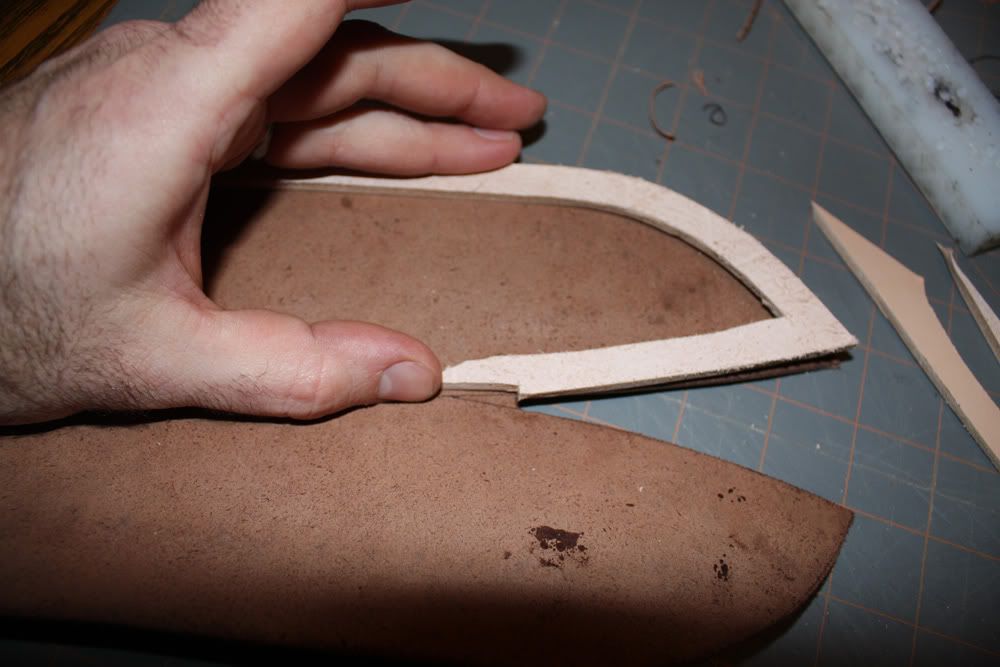
When I did it, the welt stuck out of the sheath a little, and I had to move the notch up a little to make it fit.


This looks better
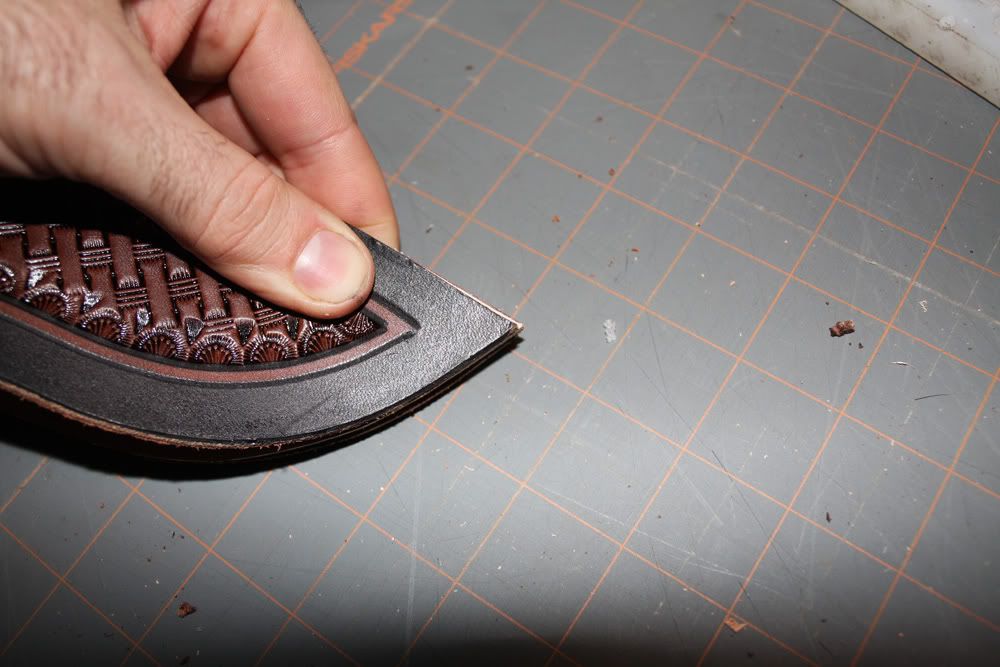
Here is where I am sure I will have the most eyebrows raised. I use rivets to hold the belt loop down. I know, I know...metal against the blade.
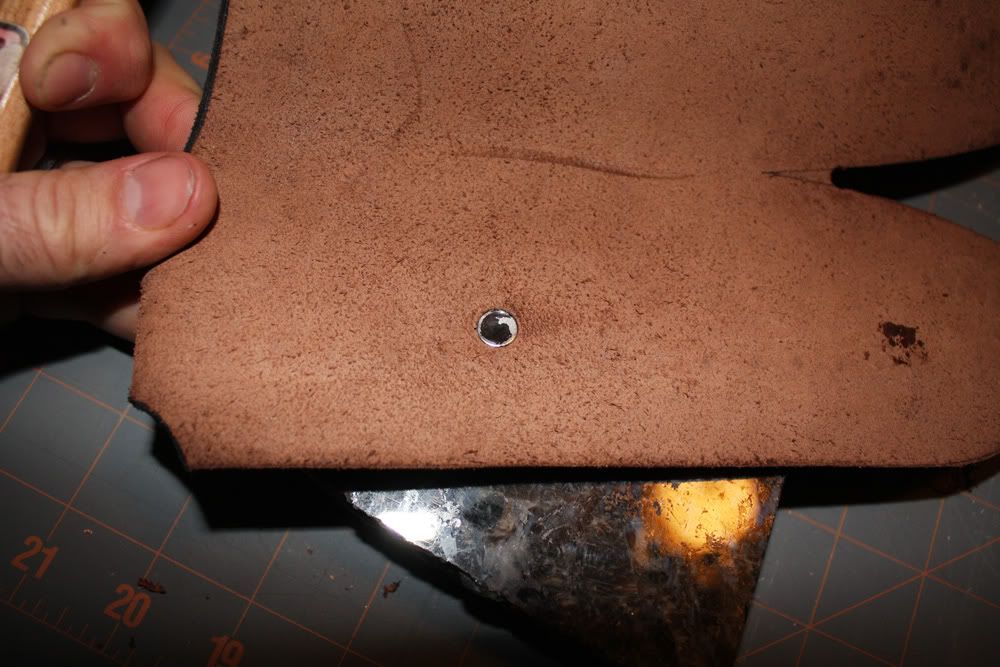
However, the hammer that I use has a convex face and when I pound the rivets from the inside, I put them a little recessed area just from pounding. I have never had a sheath returned to me or a knife for that matter because the rivets were marring the handle. Here is what I mean.

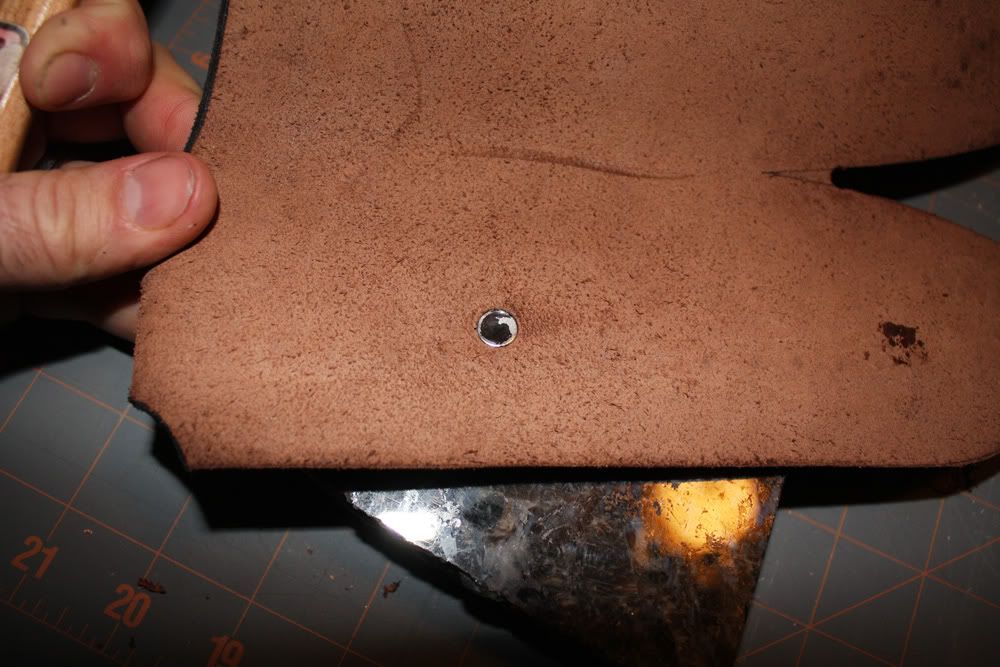
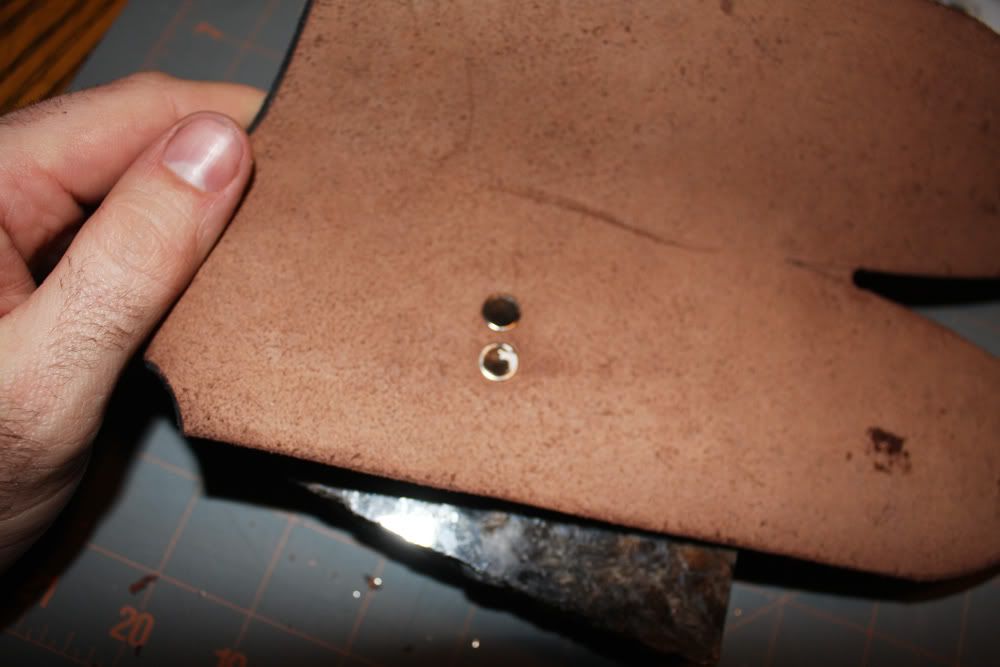

More in a bit...
Last edited: