- Joined
- Nov 9, 2006
- Messages
- 521
The primary use is to drill straight holes through the scales on slip joints. I need all the precision I can get with straight holes which seem to really impact my ability to get the blade centered in the end. Ideally, you could glue the scale onto slipjoint liner and then place the scale material on the table and drill through the liner. But the scale material has to be flat referenced to the liner. Micarta and G10 could work and I have also placed the liner on my surface grinder attachment with the scale glued on and flattened referenced to the liner. If a bolster is not flat or sits proud, or has already been profiled than this might not be possible.How does it work?
With this jig I clamp the liner and scale so the liner is facing up. Then I support this thing on two 123 blocks. Then drill through the existing hole in the liner and through the scale. Below is picture taken from the instagram of the maker who provided the idea and drawing.
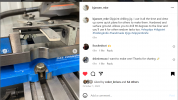