- Joined
- May 5, 2014
- Messages
- 181
Steel-Drake, thanks for follow up with nice images of maxamet edge after finished certain stone/grit.
Happy to provide them. Being able to generate data is precisely why I have a USB microscope in the first place.
My guess from angle perspective above, this would be around 80-85° (where camera is perfect vertical / perpendicular / 90°). Topographically obvious, EE surface is most flat/smooth vs others are bandy/lumpy/jagged. Without EM FOD, we can use brain to lower the viewing angle to less than 30°. Then much easier to see non-diamond affected surfaces are highly irregular dictated/sculptured by carbides. These same process, supposed/EE (or failed to/others) to create/shape the apex as flat as possible for given abrasive diameter.
Do you mean the pictures would be more useful in this case if the edge was at an angle closer to 30 degrees off of being parallel to the camera rather than ~80 degrees?
Also, just to check whether the differences in finishes between those four stones was more a result of the type of finish produced by waterstones used muddy compared to a diamond plate, or whether the difference in finishes was more attributable to the stones affecting the steel differently, I replicated the four shots above using a Mora Companion (FFG reground) I have in plain carbon steel at ~58-60 HRC:
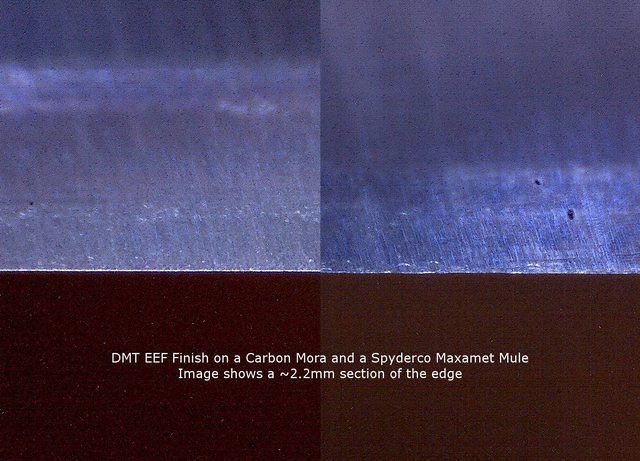
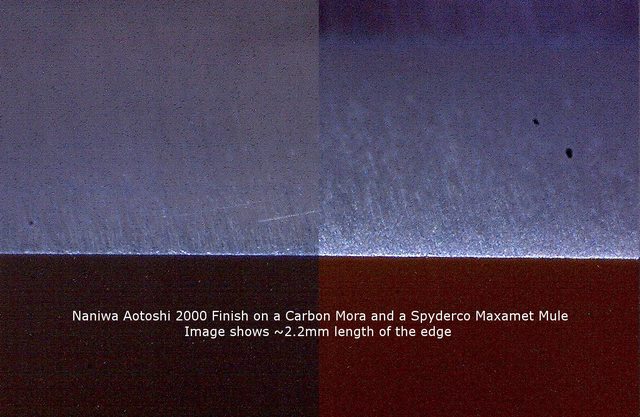

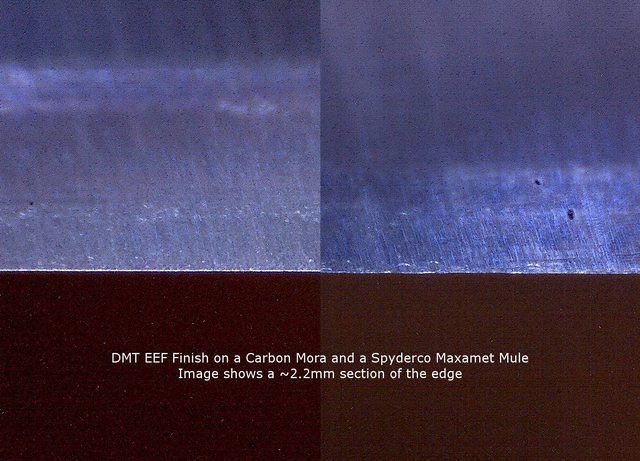
To me, the left and right halves of those images look pretty similar. Particularly in light of the extreme contrast between a plain carbon steel at ~60 HRC and Maxamet at ~68 HRC. Of course, there is still the empirical testing of the quality and strength of the apexes produced by these four stones still to come (when I can find the time), but I thought this was interesting nonetheless.
Last edited: